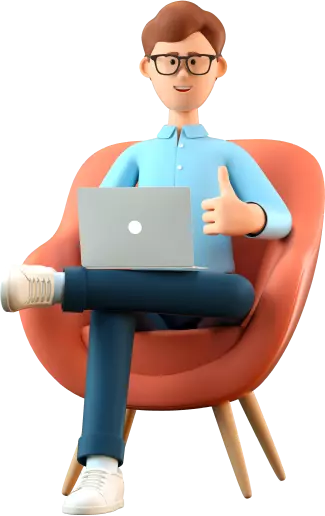
на первый
заказ
Реферат на тему: Значение и работа детали в узле и изделии
Купить за 900 руб.Введение
1 Общая часть……………………………………………………..……..1.1 Назначение и работа детали в узле…………………………………
1.2 Конструкторско-технологический анализ детали…………………
1.3 Технологические требования к детали……………………………..
1.4 Выбор типа производства…………………………………………..
2 Технологическая часть…………………………………………………
2.1 Выбор заготовки…………………………………………….……….
2.1.1 Описание типов заготовок, применяемых для данной детали…
2.1.2 Обоснование выбранного способа получения заготовки………
2.2 Разработка технологического процесса……………………………
2.2.1 Выбор маршрута обработки поверхностей……………………..
2.2.2 Разработка вариантов техпроцесса………………………………
2.3 Разработка операций………………………………………………..
2.3.1 Выбор и обоснование баз…………………………………………
2.3.2 Технологическое обоснование выбранного оборудования…….
2.3.3 Выбор технологической оснастки………………………………..
2.3.4 Проектирование операции………………………………………..
2.3.5 Расчет припусков и размеров заготовки…………………………
2.3.6 Расчет массы заготовки……………………………………………
2.3.7 Расчет режимов резания для данной операции…………………
2.3.8 Выбор режимов резания (по таблицам)………………………….
2.3.9 Техническое нормирование операций…………………………..
2.4 Заключение об эффективности спроектированного техпроцесса...
Оглавление
- Введение- Выводы
- Список литературы
- Приложение
Список литературы
Приложение А - Графическая часть курсового проекта……………….Приложение Б - Технологические документы курсового проекта……
ВВЕДЕНИЕ
Развитие промышленности во многом определяется техническим прогрессом в машиностроении.
Для промышленности необходимо повышение количества выпущенной продукции, и её качества. Этот рост осуществляется за счет модернизации оборудования на производстве.
Технологический процесс характеризуется не только улучшением конструкции машин, но и непрерывным совершенствованием технологии их производства. Важно качество, экономичность и в заданные сроки, с минимальными затратами изготовить машины.
Развитие новых прогрессивных технологических процессов обработки способствует конструированию более современных машин и снижению их себестоимости.
В машиностроении точность занимает особо важное место. Обеспечение заданной точности обработки ответственная задача конструкторов, а ее технологическое обеспечение при наименьших затратах - технологов.
1 ОБЩАЯ ЧАСТЬ
1.1 Назначение и работа детали в узле
Для передачи давления от вагона на шейки осей колесных пар, а также ограничения продольного и поперечного перемещения колесной пары служат буксы.
Устройство буксового узла.
Буксовый узел является составной частью колесной пары, монтируется и демонтируется совместно с колесной парой. Букса предназначена для соединения колесной пары с рамой тележки через надбуксовые рессорные подвешивания. Букса также является емкостью для смазки роликовых подшибников, а также предназначена для ограничения поперечного и продольного перемещения колесной пары относительно рамы тележки. Через буксу передается нагрузка от массы кузова на шейку оси колесной пары.
Буксовый узел состоит из следующих частей:
1. Корпус с приливами для крепления пружин рессорного подвешивания. На задней крышке буксы имеются кольцевые выточки, которые совместно с лабиринтным кольцом образуют лабиринт, который препятствует вытеканию смазки и попаданию пыли и грязи внутрь буксы. В приливах корпуса имеются отверстия для пропуска шпинтонов, а сверху корпуса букса отверстия для крепления датчиков СКНБ.
2. Лабиринтное кольцо является составной частью задней крышки корпуса буксы, напрессовывается на предподступичную часть оси.
3. Два роликовых подшипника, которые состоят из внутреннего кольца, сепаратора с цилиндрическими роликами, наружного кольца.
4. Упорное кольцо, установленное между роликовыми подшипниками.
5. Стопорное кольцо для крепления наружного подшипника.
6. Торцевое крепление при помощи корончатой гайки или тарельчатой шайбы.
7. Крепительная крышка.
8. Войлочные и резиновые прокладки.
9. Смотровая крышка.
Внутрь корпуса буксы заправляется консистентная смазка в количестве 3,5-4-х кг. Буксы являются наиболее повреждаемыми частями вагона и в период эксплуатации требуют постоянного контроля над своим техническим состоянием. Буксовые узлы передают нагрузки на шейки осей, обеспечивают возможность вращения колесной пары и ограничивают продольные и поперечные перемещения колесной пары относительно тележки. На пассажирских вагонах применяются буксы только с подшипниками качения (роликовыми), так как они обеспечивают реализацию высоких скоростей движения и осевых нагрузок, а также более надежны в эксплуатации.
1.2 Конструкторско-технологический анализ детали
Букса изготовлена из серого чугуна СЧ-20 ГОСТ 1412-85. В качестве заготовки используют отливку.
Отливки из чугунных сплавов составляют около 70% литья. Они обладают высокой удельной прочностью, высокими литейными свойствами, коррозийной стойкостью в атмосферных условиях. Их высокая жидкотекучесть обеспечивает получение тонкостенных и сложных по форме отливок. Линейная усадка составляет 1,0…1,25%. Формовочные уклоны выполняются по ГОСТ3212-80 за счет увеличения стенок. Сплавы имеют невысокую температуру плавления - 550…650°. Отливки из чугуна СЧ 20 - малоответственные отливки с толщиной стенок 10-20 мм (шкивы, зубчатые колеса, станины, суппорты, фундаментные плиты и др. ) ;
Обработка поверхностей может производиться стандартным инструментом.
1.3 Технические требования к детали
Технические требования к детали:
1. Точность отливки ГОСТ26645-85;
2. Допускается изготовление из чугуна СЧ-18 ГОСТ 1412-85.
3. Уклоны формовочные но ГОСТ 3212-80.
4. Неуказанные литейные радиусы 3…5 мм.
5. Неуказанные предельные отклонения размеров по ОСТ 234.209-82.
6. Маркировать обозначение, товарный знак завода-изготовителя шрифт 5 тип А без наклона по ГОСТ 2304 - 81.
7. Остальные технические требования по ОСТ 234.258-86.
8. Покрытие по ГОСТ 6572-91 система 15 эмаль ПФ-189 красная 24784-81 и У1 кроме отверстий.
1.4 Выбор типа производства
Существует три типа производства:
- массовое
- серийное
- единичное
В курсовом проектировании можно считать, что тип производства зависит от программы выпуска и трудоемкости изготовления изделия детали.
Согласно нормативам принимаем серийный тип производства.
Размер партии деталей определяют по формуле:
N=(Nа)/Ф, шт, (1)[2]
N= (200005)/244=410 (шт.)
где N-годовая программа, шт;
а - число дней запаса;
Ф-число рабочих дней в году.
Серийное производство характеризуется ограниченной номенклатурой продукции, большим объемом выпуска серий, которые периодически повторяются.
2 ТЕХНОЛОГИЧЕСКАЯ ЧАСТЬ
2.1 Выбор заготовки
Выбираем в качестве заготовки отливку.
Отливка - заготовка изделия, реже - готовое изделие, полученное при заливке жидкого материала в литейную форму, в которой он затвердевает.
Отливки подразделяются на следующие виды:
-полуфабрикаты - чушки, предназначенные для последующей переплавки;
-фасонные отливки, подвергаемые, как правило, обработке резанием;
-готовые изделия, которые только очищаются или окрашиваются.
2.1.1 Описание типов заготовок, применяемых для изготовления буксы. Букса изготавливается из серого чугуна СЧ-20 или СЧ-18 ГОСТ 1412 - 85, поэтому возможно применять вид заготовки - отливка.
Также существует возможность получения заготовки путем механической обработки резанием, но это не рационально, так как затрачивается большое количество времени, расходуется большое количество металла, некоторые контуры детали сложны для операций механической обработки, что повышает трудоемкость изготовления детали не приемлемо для среднесерийного производства.
Литье - типовой процесс-операция получения изделий, заключающийся в заполнении специальной емкости (формы), формирующей поверхность или часть поверхности изготавливаемого изделия, жидким материалом с дальнейшим термовременным переходом жидкого материала в твердое агрегатное состояние и получения, в результате, твердой заготовки, близкой по конфигурации, размерам и свойствам к изделию. Коэффициент использования материала в данном случае достаточно высок, поэтому литье является преимущественным способом получения заготовки.
2.1.2 Обоснование выбранного способа получения заготовки.
Для данной детали применяется способ литьё. В этом случае заготовка более приближена к форме самой детали. Так же этот способ характеризуется меньшей стоимостью и лучшим коэффициентом использования металла.
=ΣV*р (2)[2]
=0,35кг
=+=0,35+4,66=5,01кг
2.2 Разработка технологического процесса
2.2.1 Выбор маршрута обработки поверхностей представлен в таблице 1.
Таблица 1 - Разработка маршрута обработки поверхности
Квалитет точности
Шероховатость
Способ обработки
7 квалитет 65
Точение черновое
7 квалитет 141
Точение черновое
14 квалитет Ø80H
Точение получистовое
0.25 мм,0.37 мм
Фрезерование получистовое
0.25 мм,0.37 мм
Фрезерование получистовое
7 квалитет 4 отв. 14+0.45 мм, 0.5 мм (2 раза), мм
Сверление
В=2.2+0.2 мм
Точение черновое
2.2.2 Разработка вариантов технологического процесса.
Базовый (заводской) технологический процесс
010 Точение черновое, оправка
020 Точение черновое, оправка
030Растачивание чистовое, оборудование 1К62
040Фрезерование, оборудование 6Р13
050Фрезерование - оборудование 6Р13
060 Сверлильная, оборудование 2Н125
070Точение черновое, оборудование 1К62
Спроектированный техпроцесс
010 Точение черновое, оправка
020 Растачивание чистовое, оборудование 1К62
030 Фрезерование, оборудование 6Р13
040 Сверлильная, оборудование 2Н125
050 Точение черновое, оборудование 1К62
2.3 Разработка операций
2.3.1 Выбор и обоснование баз. Основание отливки - установочная база.
(рис.1).
Рисунок 1 - Схема базирования на операцию 010 Точение
Основание отливки - установочная база. Поверхность диаметром 80 мм - направляющая база. Заготовка лишена трёх степеней свободы (рис.2).
Рисунок 2 - Схема базирования на операцию020 Расточная
Торцевая - кольцевя поверхность диаметром 100 мм и 96 мм - установочные базы. Заготовка лишена двух степеней свободы.
Поверхность основания - установочная база(рис.3).
Рисунок 3 - Схема базирования на операцию030 Растачивание.
2.3.2 Техническое обоснование выбранного оборудования.
Токарно - винторезный 16К20
Частота вращения шпинделя, об/мин
Продольная подача, мм/об
Мощность N=10 кВт ƞ=0,75
Габаритные размеры длина ширина высота мм
Вертикально - сверлильный с плавающим столом 2Н135
Класс точности Н
Размеры конуса шпинделя по ГОСТ 25557 - 82 Морзе 4
Наибольший ход шпинделя мм 250
Расстояние от торца шпинделя мм:
-до стола 30- 750
-до плиты 700 - 4120
Рабочая поверхность стола мм 450х500
Габаритные размеры длина ширина высота
2.3.3 Выбор технологической оснастки.
Мерительный инструмент
Мерительный инструмент - это техническое устройство, используемое при измерениях и имеющие нормированные метрологические свойства. При выборе измерительного инструмента учитываются формы контроля (сплошной или выборочный масштаб производства, конструктивные характеристики детали, точность ее изготовления).
В качестве основного измерительного инструмента выбираем: Штангенциркуль.
Штангенциркуль ШЦ-1 по ГОСТ 166-80 с ценой деления 0,1 мм.
Штангенциркуль ЩЦ-1 по ГОСТ 166-80 с ценой деления 0,05 мм.
Для проверки отверстий мерительный инструмент - калибр - пробка. Так же для измерения понадобятся образцы шероховатости ГОСТ 9378.
Выбор станочного приспособления
Станочные приспособления - это дополнительные устройства к станкам, позволяющие достаточно точно устанавливать и закреплять заготовки деталей при их обработке.
При необходимости станочные приспособления обеспечивают направления режущего инструмента и периодически поворот заготовки в процессе обработки.
Станочные приспособления обеспечивают правильное взаимное расположение заготовки, стола и инструмента, расширяют технологические возможности станков. Они повышают точность обработки, производительность и экономическую эффективность, облегчают условия труда рабочих. По группам оснащаемых станков, приспособления подразделяются на токарные, фрезерные, сверлильные (кондукторы), шлифовальные и т.д.
2.3.4 Проектирование операции.
Проектирование операции 010 Токарная
Режущий инструмент резец 2110-4010 ВК8 25*16
Резец 2140-0008 ВК8 20*20
1 установить деталь в патрон, выверить, закрепить.
2 подрезать торец выдержав размеры 65±0,3.Реж.инструмент резец. ШЦ-I-125-0,1.
5 расточить фаску 0.5х45°.Реж.инструмент резец.
6 отложить деталь в тару.
2.3.5 Расчет припусков и размеров заготовки.
Расчет припуска для поверхности 80Н7 мм
На остальные поверхности припуски и допуски назначаем по ГОСТ 1505-74
Заготовка-литье
Рассчитываем припуск на черновое точение:
2=2(+h+), мм (3)[3]
где - средняя высота микронеровностей, мм;
h - глубина поверхностного дефектного слоя, мм;
- погрешность установки, мм;
- погрешность выполнения на предыдущем переходе.
Расчет припуска на получистовое растачивание:
Определяем векторную сумму пространственных отклонений взаимосвязанных поверхностей:
=√Δ+Δ, мм (4)[4]
где Δсм - смещение стержня, мм;
Δкор - коробление поверхности заготовки, мм.
Δсм=√+Δ, мм (5)[4]
где см - смещение по диаметру, мм;
Δсм - смещение по длине, мм.
Δсм=Тз/2=1,4/2=0,7 (мм) (6)[5]
где - допуск линейных размеров, мм.
Допуск линейных размеров находим по формуле (7)
Δсм=√+=0,98 (мм)
Определим Δкор:
Δкор=√+, мм (7)[7]
где Δкор - коробление по длине, мм;
Δкор - коробление по диаметру, мм.
Δкор=Δк*l, мм (8)[8]
где Δк - коробление заготовки на 1 мкм;
l -длина обрабатываемой поверхности, мм.
Коэффициенты находим по формуле (9)
Δк=1 l=80 мм
Δкор=0,001*80=0,08 (мм)
Определяем погрешность установки
=Е-Е*0,3=0,28 (мкм) (9)[2]
где Е - радиальное смещение заготовки, мкм.
Определим симметричность припуска:
2=2(0,4+√(0,98+0,28))=3026=2,8 (мм)
2.3.6 Расчет массы заготовки
m=V*р, кг (10)[9]
где V - объем заготовки, ;
р- плотность материала заготовки.
Плотность равна:
р=7,1(г/)
Объём заготовки определяем по объемной модели
Найдем массу заготовки:
=0,35кг
=+=0,35+13,21=13,56кг
2.3.7 Расчет режимов резания аналитически для одной операции.
Глубина резания
Общая глубина резания рассчитывается по формуле (14)
t=0,5*D, мм (14)[6]
Подача на оборот шпинделя станка:
s=0,1 мм/об - выбираем в зависимости от диаметра инструмента, обрабатываемого материала и его твердости.
Так как 1<10D, вводим поправочный коэффициент на глубину отверстия К=0,75.
Также вводим поправочный коэффициент на инструментальный материал К=0,6
s=0,1*0,75*0,6=0,045 (мм/об)
Уточняем величину по паспорту станка:
s=0,1 (мм/об)
Расчет скорости резания рассчитывается по формуле(15)
где -коэффициент показателей степени;
- стойкость пластинки;
- подача, мм/об;
- глубина резания, мм.
Коэффициенты:
-х=0,15
-Т=60 мин
-s=1,0 мм/об
V=34,0/***1,2=175,87 (м/мин)
Крутящий момент определяется по формуле(16)
= 10, Н/м (16)[8]
где , q, y-коэффициенты;
D - диаметр обрабатываемого отверстия, мм;
S- подача, мм/об;
- коэффициент учитывающий фактическое условие обработки.
=0,012 q=2,2 y=0,8 D=100мм s=0,1 мм/об
Так как коэффициент, учитывающий фактическое условие обработки, зависит только от материала обрабатываемой заготовки, то:
= =НВ/55 (17)[8]
= 10=1,32(Н/м)
Расчет мощности резания определяем по формуле (18)
=,кВт (18)[6]
где - крутящий момент, Н/м;
n-частота вращения шпинделя, об/мин.
- 1.32 (Н/м)
n=1000*U/П*D, мин (19)[6]
где U-скорость резания, м/мин;
П - постоянный коэффициент.
U=23 м/мин; П=3,14; D=100 мм
n=1000*29/(3,14*100)=2309 (об/мин)
Уточняем по паспорту станка:
n=1440 (об/мин)
==0,65(кВт)
Скорость фактическую рассчитываем по формуле (20)
=, м/мин (20)[5]
=3,14*4*1440/1000=18,1 (м/мин)
Определяем машинное время по формуле (21)
=. мин (21)[6]
где -длина рабочего хода, мм;
S- подача, мм/об;
n = частота вращения, об/мин.
==0,31 (мин)
Расчет вспомогательного времени находим по формуле (22)
=+++, мин (22)[7]
где - время на установку, мин;
- время на переход, мин;
- время, связанное с переходом, не вошедшее в комплекс, мин;
- время на контроль.
где t1 - время на установку и снятие детали, мин;
t2 - время на закрепление детали, мин;
t3 - время на очистку от стружки, мин.
Коэффициенты находим по [5,табл.4]
t1=0,14 мин; t2=0,17 мин; t3=0,08 мин.
=0,14+0,17+0,08=0,39 (мин)
Коэффициенты находим по [6,табл.32]
=0,02 (мин); =0,02*2=0,04 (мин)
=0,1+0,06=0,16 (мин)
=0,39+0,02+0,04+0,16=0,61 (мин)
Расчет штучного времени находим по формуле(24)
=, мин (24)[6]
где К - коэффициент серийности.
Продолжаем расчет:
К=1,07; а=4%; а=4%.
==1,05 (мин)
Расчет штучно-калькуляционного времени
Рассчитываем подготовительно-заключительное время по формуле(25)
=Т1+Т2+Т3, мин (25)[8]
где Т1-время на наладку станка, мин;
Т2 - время на дополнительные приемы, мин;
Т3 - время на получение и сдачу инструмента и приспособлений, мин.
Коэффициенты находим по [8,табл.4]
Т1=12 мин; Т2=10 мин; Т3=15 мин.
=12+10+15=37 (мин)
=+/n, мин (26)[9]
=1,05+37/100=1,42 (мин)
Норма выработки за смену рассчитывается по формуле (27)
=(480-)/,шт (27)[11]
Продолжаем расчет:
=(480-37)/=198 (шт)
2.3.8 Выбор режимов резания (по таблицам).
Выбор подачи:
Для черновой стадии:
=S*К*К*К*К*К*К*К (28)[8]
S=0,74 (мм/об)
Поправочные коэффициенты для серого чугуна выбираем по табл. 1 [10]
-механические свойства обрабатываемого материала =1,15
-состояние поверхности заготовки =1
-вылет резца =1
-геометрические параметры резца =1
-диаметр детали =0,62
-способа крепления детали =1
-инструментального материала =1,15
=0,74*1,15*1*1*1*0,62*1*1,15=0,92 (мм/об)
Для получистовой стадии определяем по формуле (29)
=*К*К*К*К*К*К*К (29)[8]
=0,52 (мм/об)
Поправочные коэффициенты выбираем по [10, табл.1]
-механические свойства обрабатываемого материала =0,85
-состояние поверхности заготовки =1
-вылет резца =1
-геометрические параметры резца =1
-диаметр детали =0,62
-способа крепления детали =1
-инструментального материала =1,15
=0,52*1,15*1*1,1*0,62*1*0,85*1=0,35 (мм/об)
Для чистовой стадии:
=*К*К*К*К*К*К*К (30)[8]
=0,25 (мм/об)
Поправочные коэффициенты выбираем по [10, табл.1]
-механические свойства обрабатываемого материала К=0,85
-состояние поверхности заготовки К=1
-вылет резца 0,85
-геометрические параметры резца К =0,8
-диаметр детали К =0,62
=0,25*0,85*1*0,85*0,8*0,62=0,09 (мм/об)
Скорость резания и мощность:
Для черновой стадии:
V=108 м/мин;Nm=5 кВт;Kvu=1.
где Kvu - поправочный коэффициент на скорость резания в зависимости от инструментального материала
Для получистовой стадии:
Vm=128 м/мин;Nm=3,4 кВт;Kvu=0,5.
Для чистовой стадии:
Vm=158 м/мин;Nm=2,6 кВт;Kvu=0,2.
Частота вращения рассчитывается по формуле (31)
n=,об/мин (31)[10]
для черновой стадии:
n= = 382,2 (об/мин)
Для получистовой стадии:
n= = 479,6 (об/мин)
Для чистовой стадии:
n= = 599,03 (об/мин)
2.3.9 Техническое нормирование операции.
Расчет нормы времени определяем по формуле (32)
=+/n, мин (32)[9]
где - штучно - калькуляционное время, мин;
- штучное время, мин;
- подготовительно - заключительное время, мин;
n - размер партии, шт.
Подготовительно - заключительное время
= ++, мин (33)[11]
где -время на организационную подготовку, мин;
-время на наладку станка, мин;
-время на пробную обработку детали.
= 9+2+2=13 (мин)
где 9 мин - получить режущий и вспомогательный инструмент в кладовой;
2 мин - на ознакомление с работой;
- на инструктаж мастера.
Установить инструмент - 2,4 мин;
Установить режимы резания - 3,2 мин;
Настроить устройство для подачи СОЖ 0,5 мин
=0,5+3,2+2,4=6,1 (мин)
=+, мин (34)[7]
где =8,2 мин.
=8,2+2,03=10,23 (мин)
Отсюда следует, что:
=13,2+8,4+10,23=31,83 (мин)
2.4 Заключение об эффективности спроектированного техпроцесса
Основным критерием определения экономической эффективности новой техники являются годовые производственные затраты.
Граница областей применения двух вариантов оборудования предназначенного для решения одной технологической операции, определённой из условия равенства приведённых затрат.
Свой вариант обозначим индексом "2", а базовый "1".
Определяем годовой экономический эффект, при составлении двух вариантов техпроцесса, по формуле (35):
где y - относительная производительность обработки;
n - коэффициент загрузки станка равный 0,85.
Относительную производительность обработки рассчитываем по формуле (36)
В=А*V0*Tпз
где А - число запусков деталей одного наименования в течении года для серийного производства А=4;
V0 - число операций обработки деталей одного наименования в одном запуске;
Тпз - подготовительно - заключительное время для токарно операции.
Продолжаем расчет:
Тпз=0,46 час
Определяем действительный фонд станка:
Ф0=4015 час
Число наименований обрабатываемых деталей на станке в течении года определяем по формуле (37):
где N - годовая программа деталей;
Тшт - штучное время обработки одной детали, мин
Годовые производственные затраты определяем по формуле (38)
С=(1+0,225*V0)Нс/а+НН/а1+М(30*RМ+7*Rэ)+Иу+Еu+Еn+Eсп (38)[9]
где Нс - норматив годовой заработной платы станочника Нс=67060
а - число станков, обслуживающих одним рабочим, а=1;
НН - норматив среднегодовой зарплаты наладчиков инструмента;
RМ - ремонтосложность механической части равна 12,5;
RЭ - ремонтосложность электрической части равна 8,5;
Иу - норматив годовых затрат на обслуживание и ремонт станка равный 706 рублей;
Еu - часть затрат, учитывающая стоимость затрат;
Еn - часть затрат, зависящих от площади под оборудованием;
Eсп - часть годовых затрат, учитывающая стоимость служебно - бытовых помещений.
Часть годовых затрат, учитывающая стоимость служебно - бытовых помещений рассчитывается по формуле (39):
Eсп=(1312+25,2*V0)*(1/а+V0*Tпз*Z/1860+1/а) (39)[9]
Eсп=(1312+25,2)*(1/1+6*4*0,46*70,3/1860)=998
Определяем годовую стоимость наладки и дополнительной оснастки по формуле (40):
В=1,45/1860*НН*А*V0*tпз+0,55*(Kпр+Kин) (40)[6]
где Kпр - стоимость специальных приспособлений, руб;
Kин - стоимость комплекта инструментов, руб.
В=1,45/1860*50819*12*1*0,46+0,55(150+40)=4235 (руб)
Относительная производительность обработки рассчитывается:
у=15/11,91=1,26
Найдём годовые производственные затраты:
С=(1+0,225*4)*(67060/1+1(30*13,5+7*8,5)+60580+4235+998=143826 (руб)
Определяем годовой экономический эффект, при сопоставлении двух вариантов техпроцесса:
Э=[2(0,85-6,24*17,5/4015)*(147433/17,5+380)-(0,79-6,24*17,5/4015)*
*(205928/17,5+4932)]*17,5=1563(руб)
Вывод:
При замене устарелых станков на более новые, производительность выросла почти в 1,5 раза, что привело к годовой экономии на 1563 рубля и экономии времени при объединении технологических операций чернового точения и фрезерования.
ЗАКЛЮЧЕНИЕ
В результате выполнения курсового проекта получены навыки изучения теоретических сведений на практике при составлении технологического процесса изготовления заданной детали. Также был приобретен опыт в работе со справочной литературой. Изучены, на примере детали Букса этапы разработки маршрутной технологи обработки, которые охватывали несколько разных операций.
Подробно зучены следующие алгоритмы, типизация которых позволяет работать с любой деталью, независимо от ее конструкторско - технологического класса: описание назначения детали и условий работы ее основных поверхностей, программа выпуска и форма организации работ, базирование, экономическое обоснование целесообразности метода получения заготовки и ее последующей механической обработки, статистическое и расчетно - аналитическое определение припусков, разработка маршрутной технологии, выбор технологического оснащения, расчет режимов резания и подсчет норм времени.
СПИСОК ИСПОЛЬЗОВАННОЙ ЛИТЕРАТУРЫ
1. ГОСТ-2.105-95 ЕСКД "Общие требования к текстовым документам"
2. Общемашиностроительные нормативы времени [Текст], М.: Машиностроение, , 2009г.
3. Андреев Г.Н. Проектирование технологической оснастки машиностроительного производства[Текст].-Под ред. Ю.М. Соломенцева. 3-е изд., М.: Высшая школа, 2009г.
4. Белорусов А.П. Проектирование станочных приспособлений[Текст], М.: Высшая школа, 2009г.
5. Станочные приспособления /Под редакцией Вардашкина Б.Н.-том 1, М.: Машиностроение, 2009г.
6. Справочник технолога машиностроителя[Текст] /Под редакцией Косилова А.Г.-том 2.-М.: Машиностроение,2009г.
7.Микятинский В.В. Точность приспособления в машиностроении[Текст].-М.: Машиностроение,2009г.
8. Режимы резания металлов. Справочник[Текст] /Под редакцией Барановского Ю.В., М.: Машиностроение,2000г.
9. Справочник технолога - машиностроения [Текст]. В 2-х томах/ Под редакцией Космоловой А.Г., Мещерикова Р.К., 4 издание М.: Машиностроение, 2008г.
10. Справочник сталей и сплавов[Текст]. Сорокин В.Г., Волоснякова Л.В., Вяткин С.А., М.: Машиностроение. 2009г.
11. Курсовое проектирование по технологии машиностроения. Методическое пособие, автор Денисенко В.Ф., 2007г.
или зарегистрироваться
в сервисе
удобным
способом
вы получите ссылку
на скачивание
к нам за прошлый год